Are the chemicals in your workplace really as safe as they seem?
Handling workplace chemicals is not as easy as it seems. The average workplace uses roughly 200 chemicals for tasks as diverse as cleaning, medical treatment, maintenance, production and testing. Understanding the uses of each of these chemicals and how to properly manage them is the goal of Canada’s national hazard communication standard – the Workplace Hazardous Materials Information System (WHMIS).
But WHMIS is not specifically tailored to the ways in which individual workplaces use potentially dangerous chemicals. As a result, many people are often unknowingly exposed to harmful chemicals that can cause medical issues like cancer, pre-cancerous tumors or respiratory disease later in life. This is a global problem that is responsible for roughly 2.4 million fatalities each year.
In developed countries like Canada, exposure to these hazardous chemicals is much more common than underdeveloped regions, meaning Canada and other high-income countries experience, on average, more occupational disease cases than lower income countries. The Workplace Safety and Health Institute estimates the cost of occupational injuries and disease to be 3% of GDP or $50 billion per year in countries like Canada.
Given the seriousness of the issue, many are working to find actionable solutions. The Ontario Ministry of Labour is launching a review on occupational cancers, which aims to analyze how to best prevent workplace diseases and how to better understand where or when they were caused. The review will provide a clearer picture of how workplace exposures can lead to occupational cancer and will help inform a new prevention strategy to further protect Ontario workers.
Industry leaders are also looking to make a difference in this space. An Ontario-based company called Rillea Technologies is developing a practical, sustainable and efficient resource to track, update and share information on hazardous workplace chemicals.
Introducing Rillea Technologies and SDS RiskAssist™ – Working to Create a Safer Workplace
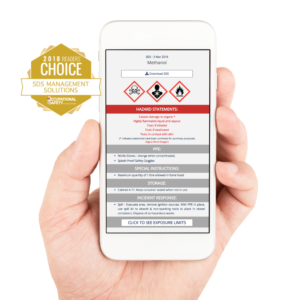
With decades of experience in both the engineering and management roles in high-risk chemical companies, the founders of Rillea Technologies understand the challenges associated with responsibly managing chemicals.
OSPE member Lisa Hallsworth, P.Eng., CEO, Rillea Technologies, and Rob Hallsworth, COO, know that even large chemical companies with resources to invest in occupational disease prevention often struggle to find efficient and sustainable ways to manage chemicals, while many smaller companies simply don’t have the resources to even try to implement a sound process or solution.
When examining how small and medium-sized business use chemicals, Rillea identified 3 significant challenges for any organization:
- The wide range of chemicals in use. There are over 144,000,000 chemical substances in existence. These can be used or combined in an infinite number of ways, meaning each organization must retrieve and review the specific information for all the products they use.
- Health hazards are invisible. Unlike those safety hazards in the workplace that can be seen, heard or felt, the health hazards associated with most chemicals display no immediate indicators of harm.
- The consequences of exposure to hazardous chemicals are not typically felt for many years or decades. This creates challenges for diagnosing the causes of related health issues.
Rillea’s research found that employers and employees faced the following obstacles when managing risk associated with chemicals:
- The Chemical Information Tsunami – WHMIS presents a lot of facts and instructions. Rillea’s research suggests that the average organization uses 200 products, which translates into over 2,400 pages of information. It would take the average person 30 minutes to read one data sheet, and they would only retain approximately 60% of what they read.
- The Bystander Effect – The bystander effect says that in group settings that require action to address a problem, most people will assume that someone else is better equipped to act. This type of scenario plays out amongst the three groups involved with the Workplace Hazardous Materials Information System (WHMIS) – suppliers, employers and workers.
Suppliers create workplace safety data sheets (SDSs). Most people would consider chemical suppliers to be the experts, but Rillea’s research shows that they are often the expert in their product, rather than how other employers are actually using it. Employers may mix the product with other chemicals, for example. As a result, many data sheets provide generic information not specific, actionable guidance.
Employers often assume that workers have read the data sheets, are aware of the hazards and will ask questions if they have any concerns. However, sightings of dust-covered WHMIS binders signal that this assumption is often false.
- A Large To-Do List – Ontario’s WHMIS regulation contains 36 actions for employers. As with most to-do-lists, only the item at the top of the list typically gets done right away – that is, updating the safety data sheets. Items lower on the list may never get started. The result is a wealth of safety data sheets in a binder, but employers themselves may not have determined how to handle hazardous products safely and workers can be left unaware of potential hazards or safe handling practices.
How Can we Tackle the Occupational Disease Problem?
To overcome the resigned lethargy that these challenges present to businesses, Rillea’s founders, both chemical engineers, knew that any process they developed to help employers must be intuitive and easy to sustain.
Based on their own workplace experiences and the requirements of occupational health and safety laws, they have developed a series of best practices for responsible chemicals management. This process is called ACT, and it is the backbone of Rillea’s new web platform, called SDS RiskAssist™.
Rillea’s ACT: A Sustainable Process for Responsible Chemicals Management
Rillea’s founders then developed algorithms based on these best practices to automate any mundane tasks in the process. Hiten Jadegja, their third partner and software engineer, then built out these algorithms in a web-based application that allows any employer – regardless of their experience level with chemicals – the ability to:
- Instantly identify their workplace chemical hazards;
- Prioritize their risk assessments;
- Create one-page chemical and workplace-specific summaries; and
- Develop chemical-specific training to help ensure employees understand how to safely use the chemicals.
Now employers can assess a chemical once and share the resulting information with all employees. Updates can easily be made to the one-page summaries and information is retained on the platform to prevent knowledge loss from any changes in personnel. The platform can also communicate through application programming interfaces (API) with other digital tools such as learning, inventory or procurement management systems.
Over 30 organizations are currently using Rillea’s SDS RiskAssist™ and have removed more than 300 carcinogens and other health hazards from their workplaces, significantly reducing the risk of occupational illness for over 5,000 workers. The platform’s data can also be analyzed across sectors to provide hazard and exposure surveillance data that may allow employers and researchers to more efficiently prevent occupational illnesses.
How does this challenge present opportunities for engineers looking to innovate?
As socially conscious technical experts, engineers are uniquely positioned to influence workplace and public safety for the better. Occupational exposure is so challenging because many chemical substances can harm us at levels so low that the human body and its senses cannot easily detect them.
With the Fourth Industrial Revolution underway, not only is technology advancing, but this is also a new frontier for safety. For instance, it isn’t too difficult to imagine how the development of wearables could be another means to keep workers safe from chemical exposure in the future.
It’s an exciting time to be an engineer. As the engineering experts behind Rillea Technologies have demonstrated, no group is better positioned to improve how we work, live and play than those who use their knowledge and skills to solve our toughest everyday challenges.
What other engineering-based workplace safety innovations have you heard about recently? Have any questions for the engineers behind Rillea Technologies? Leave a comment below.
Leave a Comment